Introduction
The number of transportation pipelines used by urban residents and industries in our country is increasing day by day, such as the maintenance and repair of various tunnel pipelines. Pipelines are common in major cities, so pipeline maintenance and monitoring are particularly important. Pipeline inspection is carried out by mounting high-definition cameras on platforms such as smart robots or drones, entering the inside of the pipeline to take video shots, and then transmitting the video signals to the ground control center through wireless video transmitter. Pipeline inspection stations are widely distributed and far apart, making it difficult to use wired communication methods. Data communication is achieved using wireless communication methods, which has the advantages of convenient installation, maintenance and migration.

User
A thermal company in northern China

Market Segment
Industry
Challenge
Routine pipeline inspections generally occur in natural gas pipelines and urban thermal pipelines. No matter what kind of pipeline or urban comprehensive pipeline corridor it is, it basically has the following characteristics:
1. The pipeline laying environment is closed.
2. The radius of the pipeline is narrow and manual inspection is impossible.
3. The pipeline is curved and in an environment where the distance is NLOS(none line of sight)
The biggest transmission obstacle encountered by robots during pipeline inspections is the shielding and obstruction of signals by the pipeline or the closed environment in which the pipeline is located, which requires wireless transmission equipment with strong non-line-of-sight capabilities.
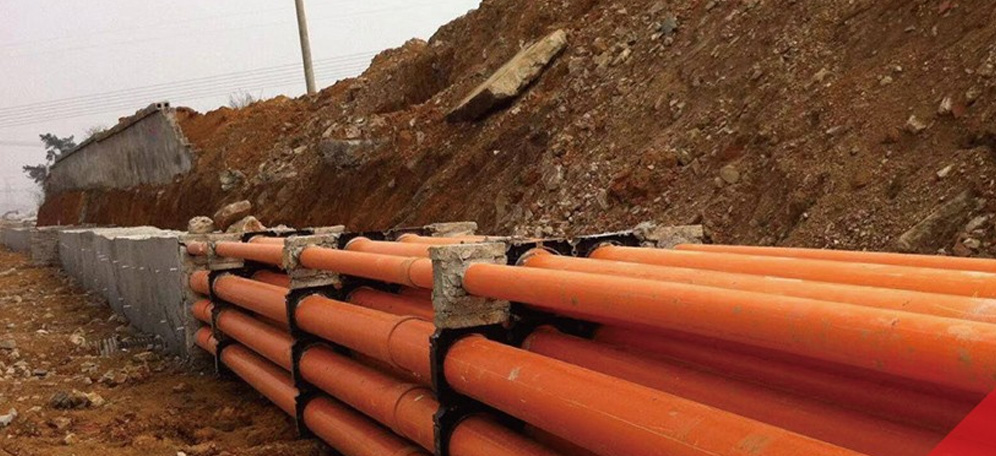
Project Introduction
The underground thermal pipe network of a city in northern China is responsible for winter heating and year-round hot water supply services for residents in some areas . This project is based on the design of a municipal thermal pipe gallery. The length of the thermal pipe network in a single area is about 1000meters , which needs to be tested before heating in winter.
Manual inspection of this thermal pipeline network every year is time-consuming, labor-intensive, inefficient, and expensive.
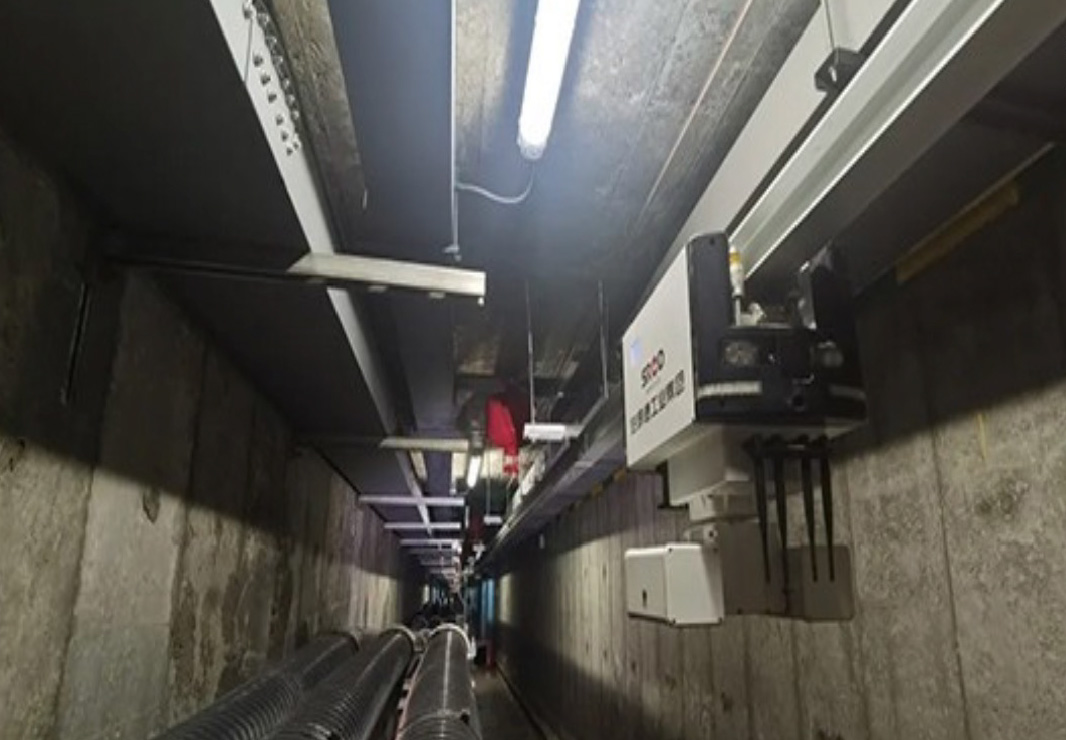
Solution
Upgrade the intelligent detection solution to transmit the internal conditions of the pipe gallery in real time to find problems in a targeted and targeted manner, making the detection more real-time, visible and convenient.
The design of the inspection system includes: installation of inspection robots, design of inspection tracks, equipped with inspection equipment and sensors, wireless video and data transmission systems, servers and control and dispatch software, measures for robots to pass through pipe corridors with certain slopes, and inspection of key areas.
During the inspection process, as the intelligent robot advances, the video footage of the pipe gallery is transmitted back to the computer of the ground inspection worker in real time through the wireless transmission equipment carried by the robot. The cameras equipped on the robot are all high-definition cameras, so the recorded videos are all high-definition videos, which requires a relatively high transmission rate of wireless transmission equipment.
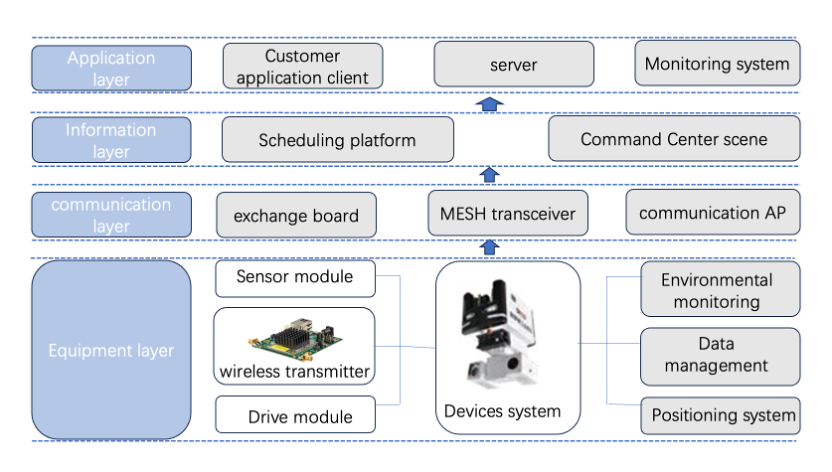
FDM-6100 is a wireless image transmission product with a transmission rate of 30M bps. It has a strong non-line-of-sight capability of 1-3 km , and can maintain real-time communication with the wireless MESH product held by the inspection worker for relay transmission. The detection pipeline distance can be further expanded.IWAVE Ultra-reliable Nlos Wireless Video Transmitters with short delay is special design for inspection robots.
The monitoring center analyzes and processes the inspection robots's working parameters, and the operator can remotely control the autonomous machine directly through the robust Mobile Ad-hoc Networks.
IWAVE long range transceiver mimo modules FDM-6100 and MESH handled terminals provide stable and reliable data communication services between the and the control center.
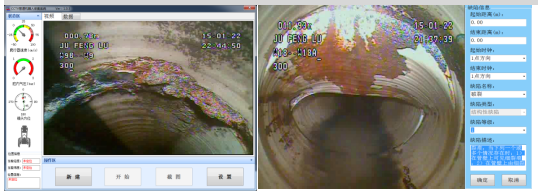
IWAVE Products in Project
Post time: Oct-13-2023